Pushing Boundaries with Automation in Next-Gen Healthcare
TESSY AUTOMATION INDUSTRIAL DIGEST
Welcome to the February edition of Tessy Automation’s Industrial Automation Digest! This month, we delve into the evolving landscape of medical device manufacturing, where innovation meets precision to redefine the boundaries of healthcare technology. From the 2024 forecast for medical device design and manufacturing to the untapped potential of legacy automation systems, we explore the pivotal trends shaping the industry. Discover how automated testing systems are pushing the limits of what’s possible, ensuring unparalleled accuracy and efficiency. We also navigate the intricate world of micro-moulding for medical devices, a testament to the industry’s drive towards miniaturization and complexity. Additionally, we highlight the strides towards sustainable production, as showcased at EMO Hannover, reflecting the sector’s commitment to environmental responsibility alongside technological advancement. Join us as we journey through these insightful developments, offering a glimpse into the future of medical manufacturing where automation is not just a tool, but a transformative force.
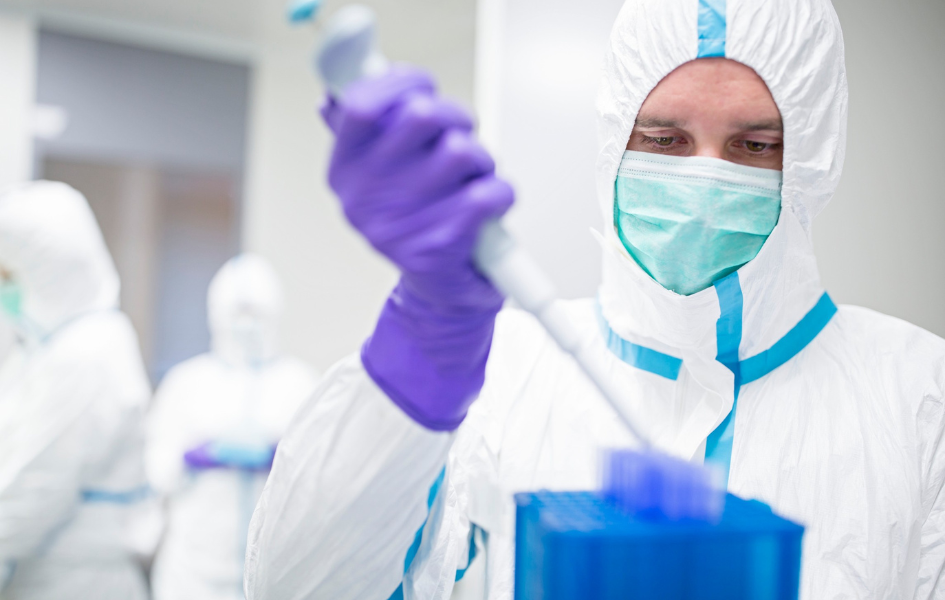
2024 Medical Device Manufacturing Forecast
The 2024 forecast for medical device manufacturing highlights significant growth, driven by an aging population and a rise in chronic diseases like diabetes and osteoarthritis. The global market, currently valued at $597.4 billion, is expected to grow at a 6.2% annual rate, reaching over $1 trillion by 2032. In the U.S., the market is set to expand from $192.78 billion to $291.04 billion by 2030. A shift towards more surgeries being performed in ambulatory surgery centers (ASCs) is part of this growth, with knee replacements in ASCs predicted to triple by 2025. This increase in procedures presents challenges, such as the need for more orthopedic surgeons to meet demand. The industry is also focusing on improving efficiency and embracing digital health solutions like AI to enhance patient care. As we move into 2024, the push for more efficient manufacturing and automation becomes crucial to keep up with these trends. Read more.
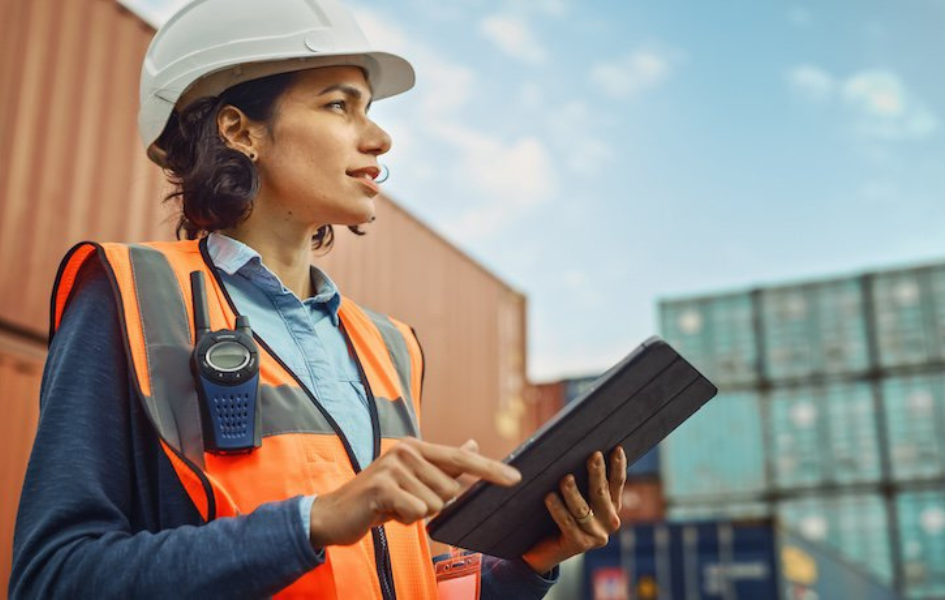
Pinpointing the Potential of your Legacy Automation Systems
Exploring the untapped potential of legacy automation systems, experts at Optimal Industrial Automation emphasize the critical need for comprehensive site surveys before upgrading. Despite the reliability of existing systems, outdated automation can lead to inefficiencies, higher costs, and potential breakdowns. The digital era demands modern, data-driven automation, leaving older systems lagging in capabilities and support. A detailed review can uncover the true state of these systems, guiding targeted upgrades to enhance efficiency and extend their service life. A case study highlights how a thorough survey identified crucial upgrades for a UK-based company, ensuring high reliability and minimal downtime, crucial for their operations. This approach not only safeguards production but also strategically directs investments towards future-proofing manufacturing processes. Continue reading.
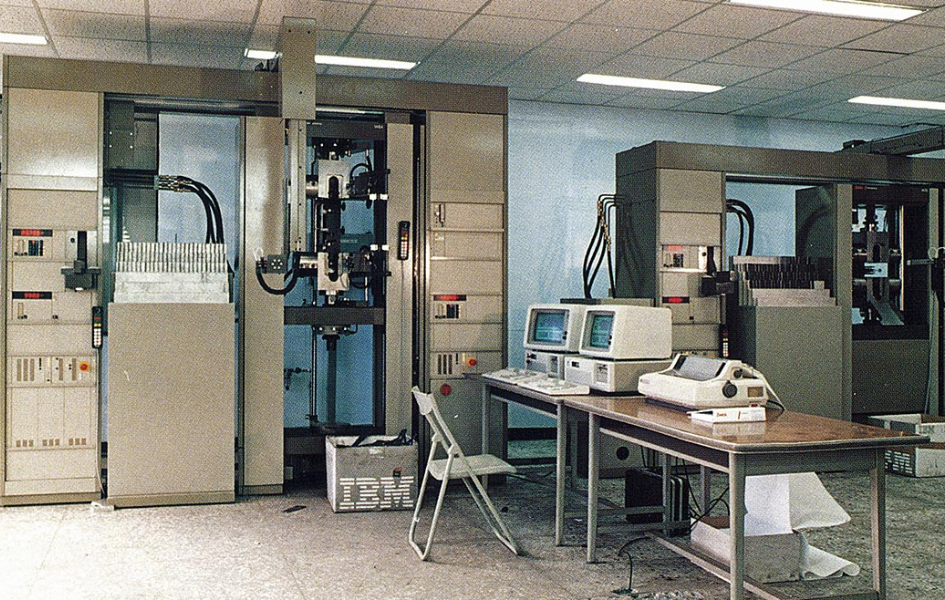
Automated Testing Systems – Pushing the Envelope
The evolution of automated testing in materials science has transformed from a niche solution for steel plants in the 1980s to a widespread necessity across various industries today. Driven by labor shortages, stringent testing standards, and the need for data security, automation now addresses challenges from handling tiny specimens in additive manufacturing to managing large, cumbersome materials. Modern systems not only automate the testing of diverse specimen sizes and types but also integrate sample preparation, expanding the capabilities of testing labs. Innovations like robots that prepare and transport samples, and systems that perform complex tests on medical devices, highlight the shift towards more sophisticated, automated solutions. While automation offers reliability and efficiency, the decision to adopt such systems balances the need for skilled labor against the investment in technology, pushing the boundaries of what’s possible in material testing. Read the full article.
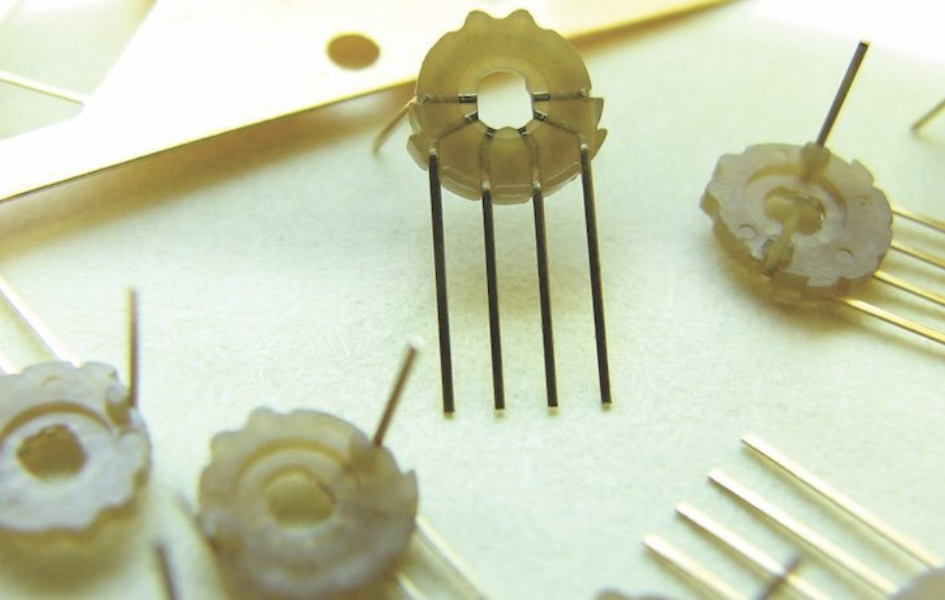
Navigating the Complexities of Micro-Moulding for Medical Devices
Micromoulding is revolutionizing the medical device industry by enabling the production of extremely small, high-precision components essential for the trend towards miniaturization in medical technology. This specialized form of injection moulding demands unparalleled precision and expertise, particularly in designing and fabricating moulds with ultra-tight tolerances. The process faces unique challenges, especially when working with biocompatible materials that require careful handling to maintain their properties and biocompatibility. Adherence to stringent quality standards, such as those set by the FDA and ISO, is paramount, necessitating advanced quality control measures and rigorous process monitoring. Innovations like 3D printing for mould creation and the use of simulation software for process optimization are pushing the boundaries of what’s possible in micromoulding. As the medical device industry continues to evolve, micromoulding stands at the forefront, driving advancements in diagnostics, treatment, and the development of smart, personalized medical devices. Keep reading.
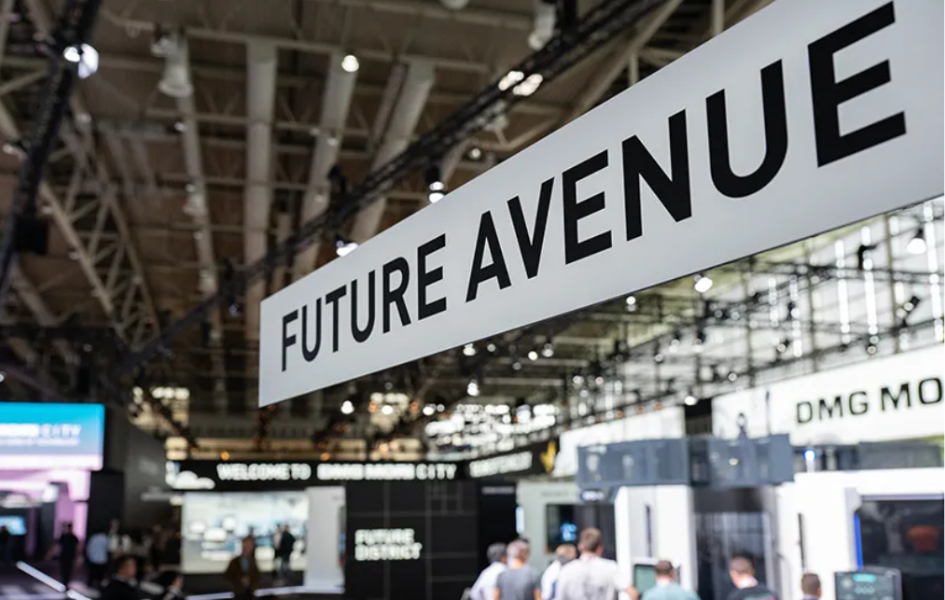
Paths to Automated, Sustainable Production
EMO Hannover 2023, under the theme “Innovate Manufacturing,” showcased the latest in automated production, sustainability, and machine networking. The event highlighted the metal industry’s response to skilled worker shortages through advanced automation and digital integration, emphasizing the importance of sustainability in production processes. Key innovations included DMG MORI’s resource-efficient machine tools designed for automated systems, Heller’s F6000 machine with its innovative features for autonomous operation, and INDEX’s modular machine tool system with comprehensive automation solutions. The fair also spotlighted cutting-edge developments like ANCA’s ultra-precise tool production and Grob-Werke’s unmanned operation systems. Additionally, the focus on sustainability was evident in CERATIZIT’s carbon footprint reporting for its products and Oerlikon Balzers’ new coating for non-ferrous materials processing. EMO Hannover 2023 demonstrated the industry’s commitment to advancing manufacturing technology, addressing labor shortages, and enhancing sustainability. Read more here.